Vehicles navigate various roads, and the road surface exerts impact loads on the wheels. Particularly when driving at high speeds on poor-quality roads, this impact load multiplies. If it is directly transmitted to the frame, it not only causes discomfort for the driver and potential damage to the goods but also inflicts harm on the vehicle components. To alleviate this impact, aside from using elastic rubber tires for shock absorption, elastic suspensions are employed to cushion the shock.
- Definition of Suspension
The suspension is the collective term for the connecting device between the frame and the axle used to convey all forces and moments. The forces and moments it transmits between the wheels and the frame minimize the road’s impact on the vehicle body, reduce the impact load on the vehicle body, dampen the vibrations resulting from road undulations, and enable the vehicle to travel smoothly.
- Classification of Suspensions
The commonly utilized elastic components in suspensions encompass various structural forms such as coil springs, torsion bar springs, leaf springs, air springs, and rubber springs. An-dràsta, leaf springs and air springs are predominantly employed in the market.
- Leaf springs are widely utilized in heavy trucks and offer numerous advantages compared to others:
(1) The structural design is straightforward, facilitating enhanced manufacturability and maintainability.
(2) It possesses a guiding function and can transmit forces and moments in all directions.
(3) The leaf springs can be combined in a specific manner to enable the leaf spring to exhibit linear or nonlinear elastic characteristics.
- Air springs are also extensively used in high-end heavy trucks at present. The spring force generated by the elastic deformation of the rubber airbag and the compressibility of the air can mitigate road impact and enhance the driving characteristics of the vehicle.
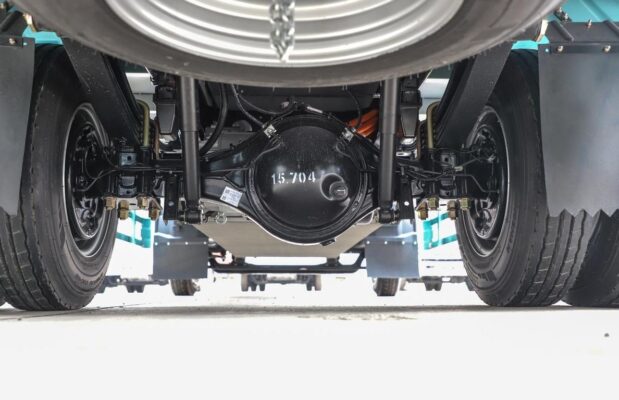
Air springs are classified into three types: bag-type air springs, membrane-type air springs, and composite air springs. Distinct from traditional leaf springs, their elastic characteristics are nonlinear and offer several advantages:
(1) High driving safety: When the vehicle traverses uneven roads, overtakes, or makes sharp turns, the stretching or compression stroke of the air spring is relatively large, and the stiffness increases rapidly to adjust the vehicle‘s balance, thereby reducing vibration and roll angle, enhancing the driving safety of the vehicle, and ensuring the integrity of the transported items.
(2) Good driving comfort: Due to the minimal internal friction when rubber and air are in operation, they can absorb high-frequency vibrations, generate less noise, and dampen the body vibrations caused by road excitation.
(3) Long service life: The service life of air springs can be as high as more than 3 million times, while the service life of leaf springs is typically only about 500,000 gu 600,000 times. The fatigue life of air springs is higher, and the usage duration is longer.
(4) Strong adaptability to working conditions: For the same type of air spring, by adjusting the internal air pressure value of the air spring, different bearing capacities can be obtained to meet the requirements of various load conditions.
Ach, the cost of equipping air spring suspensions is nearly 10 times higher than that of vehicles with ordinary leaf spring suspensions. To curtail costs, many original equipment manufacturers (OEMs) utilize leaf springs in the front suspensions of some models and air springs in the rear suspensions.
Owing to its price advantage, leaf springs remain widely adopted in various vehicles, especially in trucks. They not only ensure the high reliability of the suspension but also effectively lower the production cost of trucks.
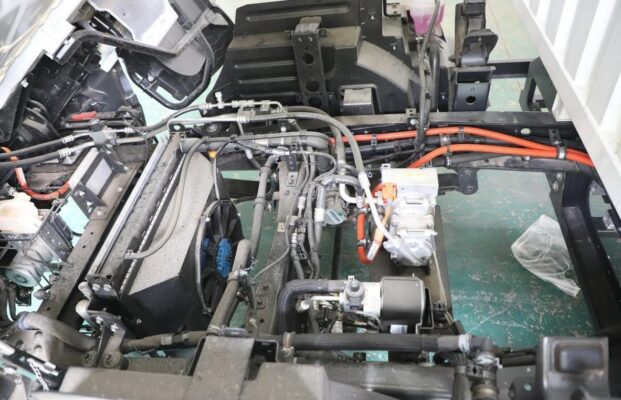
- Classification of Leaf Springs
Leaf springs are the most prevalently used elastic elements in heavy trucks. They are composed of several alloy spring steel plates with the same width but varying lengths (the thickness can be either uniform or variable). Generally, the combined strength characteristics of leaf springs are analogous to those of an equal-strength beam.
There are four common types of automotive leaf springs: multi-leaf leaf springs, few-leaf variable cross-section leaf springs, main and auxiliary composite leaf springs, and gradually changing stiffness leaf springs.
(1) Multi-leaf leaf springs: There are a significant number of leaf springs, mostly exceeding 5. The thickness of the utilized leaf springs is uniform, but the lengths differ, and the elastic characteristics demonstrate a linear alteration.
(2) Few-leaf variable cross-section leaf springs: There are fewer leaf springs, typically not more than 5. The lengths of the employed leaf springs are uniform, and the thickness varies along the length direction. The elastic characteristics exhibit a linear change.
(3) Main and auxiliary composite leaf springs: Comprised of the main and auxiliary springs in unison. When the vehicle load is modest, only the main spring operates. As the load escalates, the auxiliary spring and the main spring function concurrently, and its elastic characteristics showcase a nonlinear variation.
(4) Gradually changing stiffness leaf springs: The auxiliary spring is placed beneath the main spring. The main spring and the auxiliary spring form an integrated structure, and its elastic characteristics display a nonlinear change.
Among the above four types of leaf springs, the thickness of the leaf springs of the few-leaf variable cross-section leaf springs is engineered according to a specific rule, ensuring that the stress on the leaf springs is in an equal stress state, thereby enhancing the utilization efficiency of the spring material and achieving the objective of lightweighting the leaf springs, and it holds the most extensive application prospects.
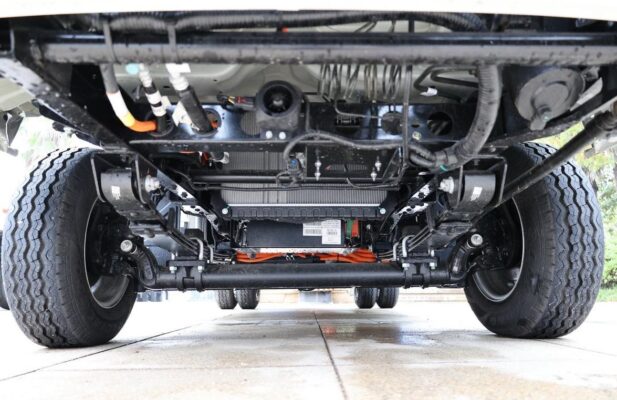
- Advantages of Few-Leaf Variable Cross-Section Leaf Springs
The lengths and widths of the leaf springs of few-leaf variable cross-section leaf springs are uniform, and the thickness varies in accordance with a certain rule along the horizontal direction. Compared to multi-leaf constant cross-section leaf springs, under identical performance conditions, it presents the following benefits:
(1) The stress distribution on the leaf springs is more uniform, approximately resembling an equal stress beam. Compared to conventional leaf springs, the weight can be effectively reduced by 30% – 40%, and the allowable stress of the leaf springs is augmented.
(2) It can diminish the dynamic stiffness of the leaf spring assembly and enhance the ride comfort of the vehicle.
(3) It circumvents the damage of the shot peening strengthening layer, can effectively enhance the fatigue strength of the leaf springs, and thereby improve the reliability of the leaf springs.
(4) Self-lubricating, friction-reducing, and shock-absorbing gaskets can be incorporated between the leaf springs, which is conducive to prolonging the working life of the leaf springs.
(5) The overall thickness is diminished, which can effectively lower the load height of the vehicle.
Now, let’s delve deeper into the future trends and potential developments in leaf spring technology and its applications in the automotive industry:
With the continuous advancement of materials science and manufacturing processes, we can expect further improvements in the performance and durability of leaf springs. New alloys and composites might be developed that offer even better strength-to-weight ratios and fatigue resistance.
Advances in computer simulation and design tools will enable more precise optimization of leaf spring geometries and configurations to meet the ever-evolving demands of vehicle performance, handling, and fuel efficiency.
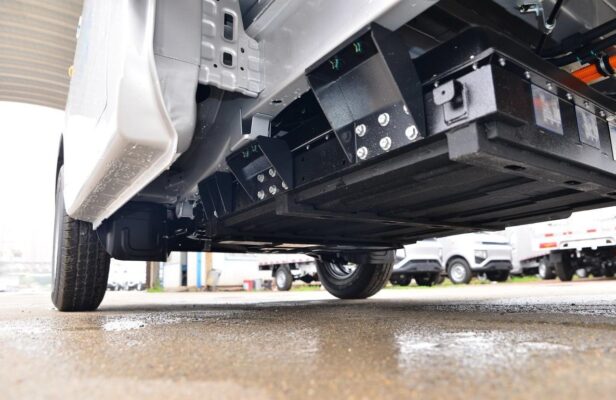
The integration of leaf spring systems with other suspension components and vehicle control systems could lead to smarter and more adaptive suspension setups. Mar eisimpleir, active or semi-active suspension systems that incorporate sensors and actuators to adjust the stiffness of the leaf springs in real-time based on road conditions and driving behavior.
In the context of electric and autonomous vehicles, the requirements for suspension systems might change. Leaf springs might need to be designed to accommodate different weight distributions and the unique dynamic characteristics of these new vehicle types.
There could also be a greater focus on sustainability in the production and disposal of leaf springs. Manufacturers might explore recyclable materials and more environmentally friendly manufacturing processes to reduce the environmental impact.
A bharrachd air, as the automotive industry becomes more globalized, standards and regulations related to leaf spring performance and safety are likely to evolve and become more stringent. This will drive innovation and continuous improvement in the design and manufacturing of leaf springs.
Finally, research into alternative suspension technologies should not overshadow the ongoing potential of leaf springs. A combined approach that leverages the strengths of different suspension types might offer the best solutions for various vehicle applications and market segments.
Ann an co-dhùnadh, while leaf springs have come a long way and offer significant advantages, there is still ample room for growth and innovation in this field to ensure they remain a vital component of vehicle suspension systems in the years to come.