This article mainly focuses on the same battery system, under the same temperature conditions and water cooling strategy, using environmental chambers of different specifications and sizes, to study the influence of different positions of the air outlet and different test layouts on the electrical performance test results of the battery system.
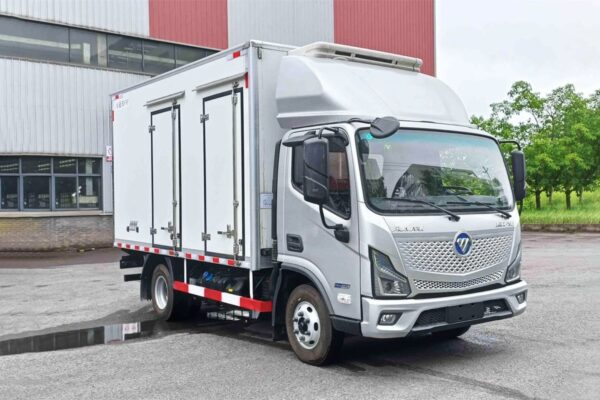
1. Theoretical Analysis
As is well known, the charging process of a lithium-ion battery is an endothermic reaction, while the discharging process is an exothermic reaction. In the initial stage of charging, the polarization internal resistance of the battery is small, and the heat generated by the internal resistance is also small. At this time, the endothermic reaction dominates, and the temperature of the battery remains basically unchanged or may even decrease slightly. In the later stage of charging, the internal resistance of the battery is large, and the heat consumption is high. At this time, the released heat is much higher than the heat absorbed by the endothermic reaction, and the temperature of the battery rises rapidly.
In a battery system, in order to ensure the service life and safe use of the battery system, each battery system has its allowable maximum temperature and minimum temperature, allowable maximum current (power), etc. During the actual operation of the vehicle, the current (power) allowed to be output by the Battery Management System (BMS) is adjusted in real time according to different State of Charge (SOC) of the battery system, different insulation states, different temperatures, different temperature differences, and other conditions. For example, if the heat dissipation is not timely and the temperature rise is high during the discharging stage, the maximum output power will be limited. If the temperature cannot be effectively reduced, when the charging starts later, the allowable maximum charging current will also be limited, and there will be a temporary phenomenon of no charging. Therefore, during the testing process of the finished battery system, the environmental conditions it is in have a great influence on the test results.
From the perspective of the internal structure, the battery cells in the battery system are surrounded by water cooling pipes, BMS, thermal management system, electrical system, etc. The heat dissipation speeds of the battery cells at different positions are not the same. For example, the battery cells near the electrical system positions such as the high-voltage interface have relatively slow heat dissipation. The different internal space volumes of the environmental chambers used and the different positions of the air outlets have a great influence on the electrical performance test results of the battery system. Therefore, it can be known from theoretical analysis that the layout method of the test setup affects the heat dissipation effect of the battery system, and there may be a large temperature deviation of the modules at different positions. In the long run, it will exacerbate the inconsistency of the modules or battery cells in the battery system, shorten the service life of the battery system, and also increase the potential safety hazards.
2. Experimental Verification
This experiment is carried out according to the electrical performance and thermal management test scheme of the battery system provided by the entrusting unit. During the experiment, the changes in the voltage, current, voltage of each single battery cell, temperature, etc. of the battery system are recorded.
In this experiment, two types of environmental chambers are used to conduct experiments on the same battery system under the same conditions, that is, operated by the same person, and using the same charge and discharge channels, the same water cooling system, and the same ambient temperature. In Experiment 1, a 10-cubic-meter environmental chamber is used, with internal dimensions of 2.5m×2m×2m. The door opening method is a full-door opening in the 2.5m direction, and the air outlet is on one side of the 2m side. The layout of the battery system is as shown in the DUT. In Experiment 2, a 15-cubic-meter environmental chamber is used, with internal dimensions of 3m×2.5m×2m. The door opening method is a full-door opening in the 2.5m direction, and the air outlet is on the 2.5m side. The layout of the battery system is as shown in the DUT, and at this time, the air outlet is perpendicular to the arrangement direction of the modules.
Under the temperature of 45℃ in the environmental chamber, the test of the charge and discharge cycle following the request signal of the BMS is started, and the test results are quite different.
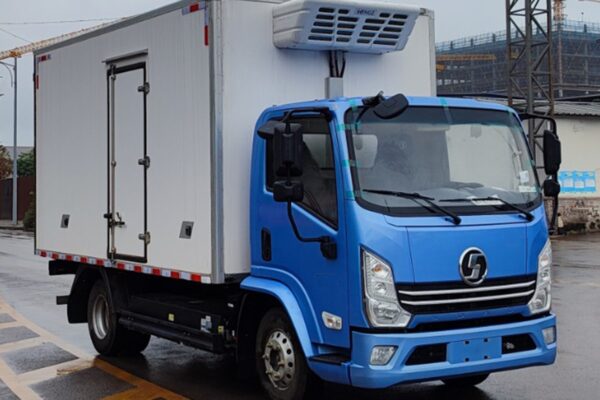
3. Result Analysis
Under the same test conditions, we analyzed the test structures of the battery systems with different environmental chambers and layout methods. During the high-temperature cycle in Experiment 1 and Experiment 2, the maximum temperature of the battery cells changed significantly. The maximum temperature of the battery cells during the cycle in Experiment 1 was 54.5℃, which was significantly higher than the maximum temperature of 53℃ in Experiment 2. And the long-term operation of the battery cells at a high temperature is not conducive to the battery condition. Therefore, we need to control and reduce the maximum temperature of the battery cells as much as possible.
On the other hand, the time taken for four cycles in Experiment 1 is almost twice that in Experiment 2. We magnified one cycle and compared the current and temperature changes of the two. It can be clearly seen that the current changes in the two experiments are very different. The time of large current charging/discharging of the battery in Experiment 1 is higher than that in Experiment 2, and the current in the initial stage of charging in Experiment 1 almost remains around 0.
When the discharging in Experiment 1 ended, the maximum temperature of the battery cells in the battery system reached 53.5℃, which was close to the allowable maximum temperature of the battery system. At this time, the allowable charging current of the vehicle’s BMS was basically 0. As the temperature decreased, the allowable current (power) of the vehicle gradually increased. However, the 10-cubic-meter environmental chamber and its layout method were not conducive to heat dissipation, resulting in the temperature rise of the battery cells again, and the charging current decreased again. When the discharging in Experiment 2 ended, the maximum temperature of the battery cells was 51℃. The 15-cubic-meter environmental chamber fully ensured heat dissipation, and the charging process was an endothermic reaction, which reduced the temperature of the battery system. The allowable charging current of the vehicle was relatively large. In the later stage of charging, as the SOC of the battery system increased, the allowable charging current gradually decreased until it reached the fully charged state.
It can be seen from the experimental data that for the same cycle, the time taken in Experiment 1 is almost twice that in Experiment 2. This is because the heat dissipation of the incubator in Experiment 1 is poor, the temperature of the battery cells is high, and the allowable charging current following the BMS is limited, so the time of one cycle is greatly extended. This result further proves that the differences in the external environment and layout methods have an impact on the electrical performance of the overall battery system. The larger the space, the more conducive it is to the heat dissipation of the battery cells and to reducing the maximum temperature of the battery cells.
At the same time, we compared the temperature differences of the two groups of experiments. The maximum temperature difference in Experiment 1 was 6℃, which occurred when the temperature of the battery cells in the battery system reached the maximum temperature, and then it basically remained between 4.5-6℃. In Experiment 2, the maximum temperature difference was about 5℃, which also occurred near the maximum temperature point, and basically remained within 2.5℃ in the later stage of charging. A smaller temperature difference indicates that the consistency difference of the overall battery cells inside the battery pack is small, and the overall service life of the battery system is relatively long.
We further carried out a detailed analysis of the temperature distribution inside the battery system. There was a temperature stratification at each temperature point in Experiment 1. The temperature of several temperature points of the upper module differed by up to 6℃ from other temperature points, and the temperature difference between the two layers was about 2℃. The temperature of each temperature point in Experiment 2 was concentrated within a certain temperature range, and there was no obvious temperature stratification phenomenon. We know that the temperature points at various places in the battery system represent the temperature rise conditions of the corresponding modules or battery cells. The occurrence of temperature stratification will lead to inconsistent temperatures at various places in the subsequent use, a relatively large temperature difference, which will affect the performance and service life of the battery cells, cause poor consistency of each battery module and battery cell in the battery system, and ultimately affect the performance and service life of the battery system. The phenomenon of relatively concentrated temperature in Experiment 2 indicates that the consistency of the modules and battery cells inside the battery system is good, ensuring the normal use of the battery.
In recent years, the situation of electric vehicles catching fire and burning has occurred from time to time, which makes consumers dare not easily buy electric vehicles to a certain extent. Therefore, the GB38031-2020 standard has added the thermal runaway expansion test in the safety test of power batteries, requiring that the time from triggering the thermal event alarm signal to the fire and explosion should not be less than 5 minutes, that is, to ensure that passengers have enough escape time. There are two recommended thermal runaway triggering methods in this standard: needle penetration triggering and heating triggering.
Both methods of triggering thermal runaway are to increase the temperature of part of the battery to reach the conditions for thermal runaway, and then spread it to other battery cells. The inconsistency of the battery modules and battery cells will accelerate the occurrence of thermal runaway. The electrical performance of the battery that has been operating in a high-temperature area for a long time decays rapidly, the internal resistance of the battery increases, the temperature rise under the same conditions accelerates, the power performance decreases, and the ability to withstand large current charging and discharging decreases. Under the same working conditions, some batteries will have overcurrent situations, resulting in phenomena such as fire and explosion during the later use, threatening the safety of consumers and property.
From the above experimental results, when the battery system is actually installed in an electric vehicle, it is also necessary to consider its heat dissipation space and the relative position with the air outlet accordingly, so that the battery system can maintain the consistency of its battery cells and modules as much as possible on the basis of good heat dissipation, and improve the electrical performance, service life, and safety of the battery system.
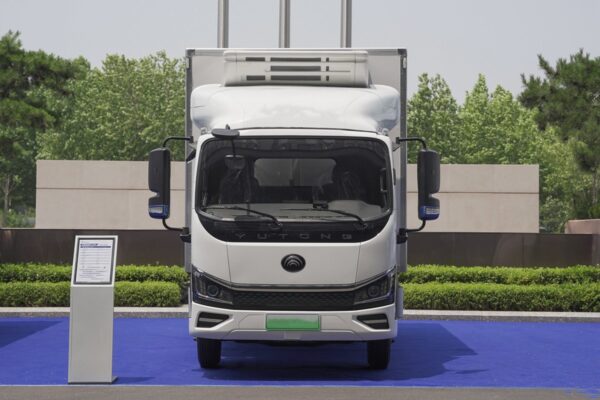
4. Conclusion
The performance of the power battery system affects the development of the electric vehicle industry. It is necessary to analyze from the battery mechanism in combination with the actual use requirements of the whole vehicle and carry out experimental research with reference to the corresponding standards. This experiment mainly studied the same power battery system sample, under the same water cooling conditions, using environmental chambers of different specifications and different positions of the air outlet for layout. The results show that:
- The environmental chamber with a larger space volume is more conducive to the heat dissipation of the battery system, and the temperature rise is lower.
- When the position of the air outlet is perpendicular to the arrangement direction of the modules, the temperature rise of the battery system is lower, and there will be no temperature stratification phenomenon between the modules.
- In the installation of the whole vehicle, it is recommended that we consider both the heat dissipation space of the battery system and the relative position with the air outlet to improve the electrical performance, service life, and safety of the battery system.