- Preface
In recent years, new energy vehicles have been booming under the guidance of national policies. ამჟამად, most electric commercial vehicles, such as pure electric buses, pure electric logistics vehicles, and pure electric road sweepers, adopt pneumatic braking systems and pneumatic door control systems. The electric air compressor system (hereinafter referred to as the electric air compressor system) provides the air source for the vehicle’s pneumatic braking system and other auxiliary air-consuming systems, and it is one of the essential key systems for electric commercial vehicles. The matching design of the electric air compressor system will directly affect the safety, comfort, cost, and energy consumption of the entire vehicle. Therefore, when designing, it is necessary to match a suitable electric air compressor according to the requirements of the entire vehicle and adopt a reasonable control strategy.
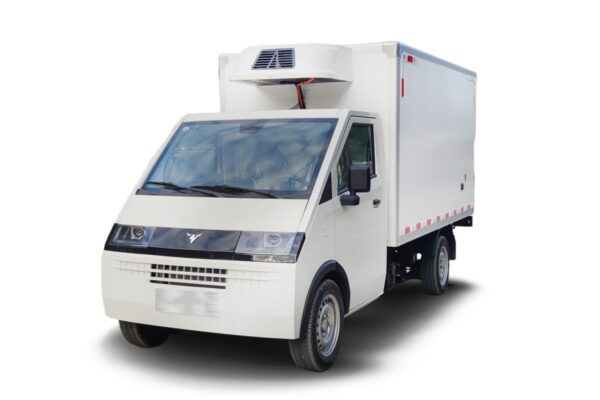
- Contents of the Matching Design
The electric air compressor system includes an electric air compressor, a motor controller, an air treatment unit, transmission pipelines, high and low voltage lines, და ა.შ.. Among them, the electric air compressor is composed of a motor and an air compressor. This article takes a certain pure electric logistics vehicle as an example to introduce the matching design of the electric air compressor system.
2.1 Matching Design Objectives of the Electric Air Compressor System
The matching design objectives of the electric air compressor system include performance, comfort, and durability.
The performance objectives include exhaust pressure and volumetric flow rate. According to the requirements of the vehicle’s braking system and the national standard GB 7258, the exhaust pressure should not be less than 0.95MPa. According to the requirements for the charging time of the vehicle’s braking system in GB12676-2014 and the total volume of the air storage tank, it can be calculated that the volumetric flow rate should not be less than 150L/min.
The comfort objective mainly refers to the noise of the electric air compressor. Since there are currently no relevant noise limit standards for ელექტრო მანქანაs to refer to, by benchmarking the electric air compressors with relatively low noise in the market, such as vane type and screw type electric air compressors, it is determined that when the electric air compressor is tested according to the method required by GB/T 4980, the noise should not be greater than 72dB.
The durability objective is that after a 500-hour durability test according to the requirements of QC/T 29078, the decrease in volumetric efficiency and volumetric flow rate should not be greater than 6%, and the oil discharge with the gas should not be greater than 0.08g/m³.
2.2 Selection of the Air Compressor
According to the different types of air compressor pump heads, electric air compressors can be divided into vane type, screw type, scroll type, reciprocating piston type, rocking piston type, და ა.შ.. Different types of electric air compressors have different advantages. Considering its performance, comfort, reliability, cost, და ა.შ.. comprehensively, the piston type electric air compressor is selected for this pure electric logistics vehicle. It has the advantages of high exhaust pressure, maturity, reliability, and low cost, but it also has the problem of relatively large noise.
2.3 Overall Design
According to the structural differences between the air compressor systems of traditional vehicles and ელექტრო მანქანას, the preliminary overall design schematic diagram of the electric air compressor system is drawn. In traditional vehicles, the air compressor is driven by the engine. In ელექტრო მანქანას, the air compressor is driven by a small motor. The power battery provides energy for the motor, and the motor controller drives the motor to operate according to the planning of the control strategy.
2.4 Performance Design of the Electric Air Compressor System
2.4.1 Main Structural Parameters of the Air Compressor
According to the generalization principle, the same cylinder diameter and stroke as the existing piston type air compressors for traditional vehicles are adopted, that is, 65×38(მმ). According to the structural characteristics of the piston type air compressor, in order to obtain better dynamic balance performance, it is advisable that the number of air compressor cylinders is equal to or more than two. In this case, an in-line twin-cylinder structure is adopted.
Due to the needs of structural design, when the piston reaches the top dead center, the compressed air in the cylinder cannot be completely discharged, that is, there is a clearance volume. The equivalent clearance stroke is taken as 3mm.
The main structural parameters of the air compressor in this case are shown in Table 1.
2.4.2 Motor Matching
The main function of the motor is to drive the air compressor pump head to operate. According to the technical parameters calculated from the performance of the air compressor, when matching the motor, the parameters such as the power, speed, and torque of the motor are mainly considered.
According to the performance calculation parameters of the air compressor, the driving power of the air compressor is 1.303kW. According to the motor power grade, 1.5kW is selected, the speed is 1200r/min, and the peak torque is 40N·m.
The rated voltage of the motor needs to be adapted to the voltage platform of the energy storage system. საერთოდ, there are two specifications of 220V and 380V. In this case, the battery voltage platform exceeds 500V, so the rated voltage of the selected motor is 380V. At the same time, in order to meet the “Technical Conditions for the Safety of Electric Buses”, the IP protection level, insulation level, და ა.შ.. of the motor also need to be considered. In this article, the protection level of IP67 and the insulation level of H grade are finally selected.
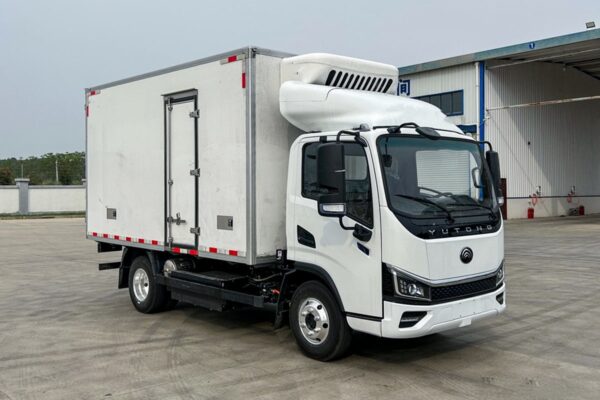
2.5 Noise Reduction Design of the Electric Air Compressor System
Pure electric vehicles are relatively quiet during operation, but the operating noise of the piston type electric air compressor is relatively large. საერთოდ, the operating noise of the piston type air compressor can reach 80~85dB, which seriously affects the comfort during the operation of the entire vehicle. Therefore, noise reduction design is required during matching. The noise of the piston type electric air compressor is mainly divided into intake noise, exhaust noise, mechanical vibration noise, and motor noise, among which the intake noise and exhaust noise are particularly prominent.
2.5.1 Intake Noise
During the operation of the air compressor, due to the intermittent opening and closing of the suction valve, the air is also intermittently sucked into the cylinder. Therefore, a pressure pulsating airflow is formed in the intake pipe and radiates from the air inlet in the form of sound waves, which is the intake noise. The fundamental frequency of the intake noise f = 2n/60, where n is the motor speed, and f = 40Hz. In addition, there are higher harmonics such as 2f, 3f…, so the intake noise has obvious low-frequency characteristics.
In this case, the intake noise is reduced by using an intake muffler. For the low-frequency characteristics of the intake noise, a reactive expansion muffler is adopted.
2.5.2 Exhaust Noise
When the compressed gas is intermittently discharged from the exhaust valve of the air compressor, the gas vibrates around the exhaust port, thus generating exhaust noise.
In this case, the exhaust noise is reduced by setting Helmholtz resonators in the exhaust cavity of the cylinder head. The Helmholtz resonator is a closed body with a hard surface inside, connected to a narrow neck-shaped channel so that the sound waves can enter the closed body through the narrow channel. The air column in the neck vibrates violently due to resonance, consuming the energy of the sound waves. The Helmholtz resonator can consume the sound waves within a specific frequency range. The frequency of the consumed sound waves is determined by the volume V of the resonator, the diameter d of the neck, the length l of the neck, and the sound speed c.
A total of 6 Helmholtz resonators are set in the exhaust cavity of the cylinder head of the air compressor. The volume of the resonator is determined according to the spatial structure of the cylinder head. According to the noise frequency range basically between 700~800Hz, the calculated diameter d of the small hole is 2~3mm.
2.6 Testing of the Electric Air Compressor Assembly
The testing of the electric air compressor assembly is to test the exhaust pressure, volumetric flow rate, noise, durability, და ა.შ.. on the test bench. The electric air compressor system also needs to be tested on the actual vehicle, such as communication matching, control matching, overall efficiency and energy consumption, vibration, და ა.შ.. This article mainly introduces the testing of the assembly.
In this case, the exhaust pressure and volumetric flow rate testing of the electric air compressor assembly is carried out according to GB/T 3853, and the noise testing is carried out according to GB/T 4980. The main results are shown in Table 2, which meet the standard requirements.
After the durability test is carried out for 500 hours according to the requirements of QC/T 29078, all performance indicators meet the standard requirements, achieving the design objectives.
The bench test of the electric air compressor also includes test items such as exhaust temperature, volumetric efficiency, volumetric specific energy, sealing performance, oil discharge with the gas, lubricating oil consumption, vibration intensity, and low-temperature starting performance, which will not be elaborated here.
- Control Logic of the Electric Air Compressor System
The control strategy of the electric air compressor system needs to focus on the braking safety and the safety of the electric air compressor, and try to reduce the energy consumption.
The air compressors of traditional vehicles are in the unloading state for most of the time, wasting a lot of energy. In this case, the energy consumption is reduced by controlling the start and stop of the electric air compressor.
When the pressure in the vehicle’s air storage tank reaches the pressure required by the braking system, the electric air compressor should be stopped to save the electrical energy of the entire vehicle. When the pressure in the air storage tank is lower than the pressure specified by the braking system, the electric air compressor should be started. At the same time, in order to extend the service life of the air treatment unit and avoid water accumulation in the air circuit, the control strategy of the electric air compressor system should take into account the backblowing and regeneration function of the air treatment unit. In this case, a high level of the electronically controlled air treatment unit indicates that the pressure in the air storage tank is too low, and a low level indicates that the pressure in the air storage tank has reached the pressure required by the braking system, and the air treatment unit has completed the backblowing and regeneration function.
The lubricating oil pressure of the electric air compressor needs to be monitored during its operation. If the oil pressure cannot be detected within 30 seconds after the electric air compressor is started, a fault should be reported to the vehicle controller and the compressor should be stopped. The oil pressure signal is fed back to the vehicle controller through the oil pressure sensor on the electric air compressor.
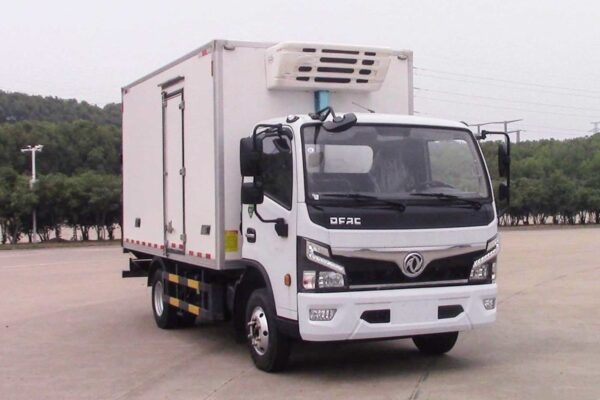
- დასკვნა
With the promotion and popularization of electric vehicles, the application of the electric air compressor system is becoming more and more widespread. In the actual design work, the reliability, comfort, cost, and energy consumption of the electric air compressor system should be fully considered according to the requirements of different vehicle models, and theoretical calculation and experimental verification are both indispensable. This article takes a certain pure electric logistics vehicle as an example to illustrate the contents and methods of the matching design work of the electric air compressor system.
At the same time, there is currently a lack of a unified technical standard for electric air compressors in the automotive industry. Each air compressor manufacturer uses national standards, mechanical industry standards, or traditional air compressor standards for design and testing. This leads to inconsistent comparison standards for products from different manufacturers, resulting in a waste of testing resources for vehicle manufacturers. The author believes that the technical condition standards for electric air compressors in the automotive industry should be introduced as soon as possible.