Dump truck diesel engines are mostly equipped with gear-type oil pumps, which are installed in the oil pan of the engine and consist of components such as the pump body, pump cover, pump shaft, and driving and driven gears. The end face of the pump cover is equipped with an oil discharge groove and an oil return hole for the oil cylinder. The oil discharge groove is used to eliminate the trapped oil phenomenon; the oil return hole is to return the excessive oil overflowing from the pressure-limiting valve back to the oil inlet cavity of the oil pump.
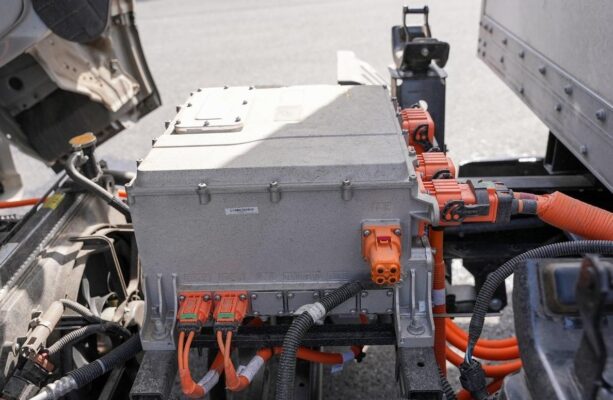
During the maintenance of the oil pump, its end clearance should be inspected and measured, which is generally within 0.07 – 0.16mm. If it exceeds this range, the end face adjustment gasket can be removed to adjust the clearance and restore it to the normal value. However, it must be ensured that after the oil pump is assembled, the driving shaft can rotate flexibly without jamming. During the operation of the engine, if the oil pressure suddenly drops or rises, it is generally caused by the sticking of the pressure-limiting valve. The pressure-limiting valve should be removed for cleaning the valve hole and the valve body; for new machines, it should be checked whether there are processing iron filings or other impurities causing jamming, and it should be removed and reassembled.
The overhaul of the main components of the gear-type oil pump has the following points: First, the inspection of the inner cavity surface of the pump body and each joint plane. During disassembly and inspection, special attention should be paid to whether there is any damage on the pump cavity surface and each joint surface. If slight scratches are found on the pump cavity, they can be repaired with fine sandpaper. If there are severe scratches, it should be replaced. The joint surface of the pump cover should be kept flat. If the joint surface of the pump cover shows severe wear, it can be repaired with a surface grinder. Second, measure the fit clearance between the top of the gear teeth and the inner wall of the pump housing with a feeler gauge. This clearance is generally 0.13 – 0.25mm. If the clearance on one side exceeds the limit value, the driving gear and the driven gear must be replaced, or the oil pump assembly should be replaced. Third, measure the end face clearance between the gear and the pump cover by using a ruler and a feeler gauge. Generally, it is 0.02 – 0.124mm. If it exceeds 0.15mm, the gear should be replaced. For oil pumps with adjustment gaskets installed between the pump cover and the pump body, gaskets of different thicknesses can be used to adjust the clearance. If the end face has slight scratches, it can be repaired with an oilstone. Fourth, measure the meshing clearance of the gears with a feeler gauge. During measurement, detection should be carried out at three points where the gears are 120 degrees apart from each other. Generally, the gear meshing clearance is 0.05 – 0.25mm. If it exceeds the limit value, the gears should be replaced. Fifth, detect the clearance between the driving shaft and the oil pump housing with a dial indicator. Generally, it is 0.05 – 0.15mm, and the limit value is 0.20mm. If the driving shaft and the pump housing are severely worn, the coating method can be used for repair. Sixth, measure the fit clearance between the driven shaft and the bushing. Generally, it is 0.06 – 0.14mm. If it exceeds the limit value (0.15mm), the bushing or the driven shaft must be replaced.
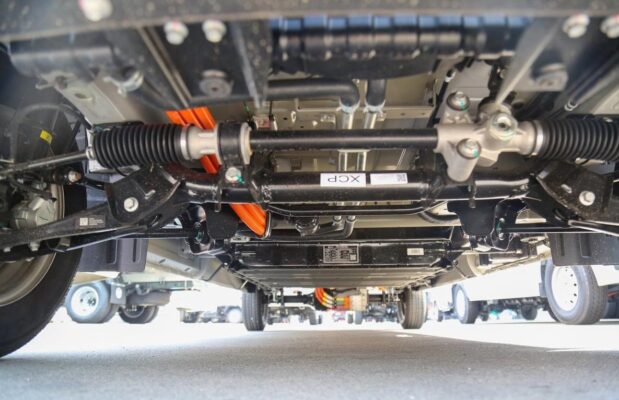
Let’s consider a scenario where a dump truck has been experiencing inconsistent oil pressure, and upon inspection, it is discovered that the gear-type oil pump requires an overhaul. The technician begins by carefully disassembling the pump, noting the condition of each component as it comes apart.
When inspecting the inner cavity surface of the pump body, they find some minor scratches. Using fine sandpaper, they gently smooth out these marks, ensuring that the surface is once again smooth to prevent any disruptions in oil flow. However, if the scratches were deep and extensive, replacing the pump body would be the only viable option to ensure proper functioning.
Measuring the fit clearance between the top of the gear teeth and the inner wall of the pump housing reveals that one side is beyond the acceptable limit. In this case, new driving and driven gears are procured and installed to restore the optimal clearance and prevent excessive oil leakage or insufficient pressure.
The end face clearance between the gear and the pump cover is measured next. If it exceeds the maximum allowable value, the technician either replaces the gear or selects an appropriate adjustment gasket to bring the clearance back within the specified range. Even a slight scratch on the end face is addressed carefully with an oilstone to ensure a proper seal.
When checking the meshing clearance of the gears, if it is found to be too large, replacing the gears becomes necessary. This ensures efficient power transmission and consistent oil pressure throughout the engine’s operation.
The clearance between the driving shaft and the oil pump housing is measured with a dial indicator. In cases of severe wear, the coating method is employed to restore the shaft to its original dimensions and ensure a snug fit within the housing.
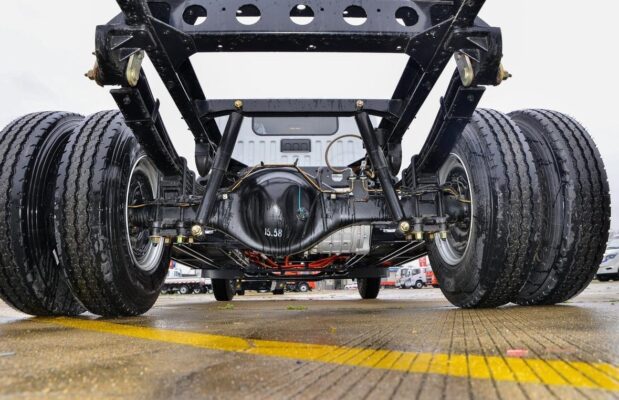
Finally, the fit clearance between the driven shaft and the bushing is evaluated. If it exceeds the limit, either the bushing or the driven shaft is replaced to maintain the proper alignment and smooth rotation of the shaft.
Now, let’s delve deeper into some of the potential complications that could arise during the overhaul process.
Suppose the technician fails to accurately measure the clearances or misinterprets the measurement results. This could lead to improper assembly, resulting in continued oil pressure issues or even premature failure of the oil pump. For example, if the meshing clearance of the gears is not set correctly, it could cause excessive noise, increased wear, and reduced efficiency of the pump.
Another potential problem could be the availability of replacement parts. If the exact specifications of the driving or driven gears are not in stock, it might lead to delays in the repair process or the use of non-genuine parts that may not meet the quality and performance standards.
In a real-world example, a dump truck operator ignored early signs of inconsistent oil pressure and continued to operate the vehicle. This led to severe damage to the gear-type oil pump, requiring extensive repairs and a longer downtime. Not only did this result in significant repair costs, but it also affected the truck’s productivity and revenue generation.
In the future, as technology progresses, we might see advancements in the design and materials of gear-type oil pumps for dump trucks. This could lead to increased durability, improved efficiency, and potentially reduced maintenance requirements. For instance, the use of self-lubricating materials or advanced coatings could minimize wear and extend the service life of the components.
Furthermore, diagnostic tools and techniques might become more sophisticated, allowing for earlier detection of potential issues and more accurate assessment of component wear. This would enable proactive maintenance and prevent major breakdowns.
In conclusion, the overhaul of the main components of the gear-type oil pump for dump trucks is a meticulous process that requires precise measurements, attention to detail, and the use of quality parts and tools. By following the correct procedures and addressing any potential challenges promptly, the reliability and performance of the oil pump can be restored, ensuring the smooth operation of the dump truck‘s engine and minimizing the risk of costly breakdowns and disruptions to operations.