After being used by users, it was found that transverse cracks emerged near the welding part of the support plate and the subframe of the XQD314OG6D 7.5T dump truck, and the weld at the connection between the support plate and the middle crossbeam was fractured (Figure 1). After the user added a plate by welding at the crack, the crack appeared again at the connection between the plate and the subbeam. In the spirit of being responsible to the users, the following is an analysis of the causes of the crack and the weld fracture.
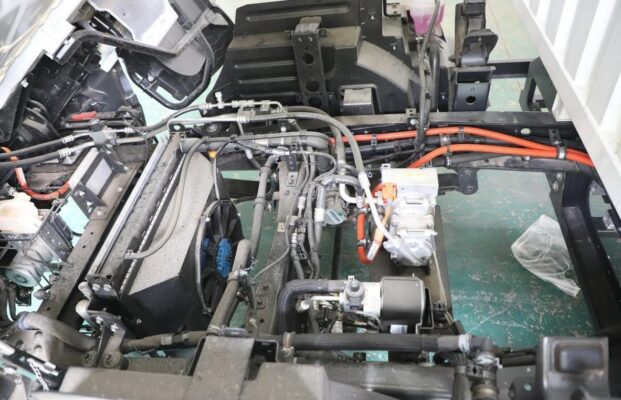
- Reasons for Cracking
1.1 The chassis used for this dump truck was modified from an EQ1l41GJ (wheelbase 4.5m) ordinary truck. The modified dump truck is mostly employed for earth, stone engineering and coal mine transportation, and its working conditions are extremely harsh. The rated capacity is 7.5t, but in actual use, it is overloaded to approximately 11t. At this juncture, the bending stress and torsional stress endured by the frame and the subbeam are significantly greater than those of ordinary trucks.
1.2 When the dump truck compartment is fully loaded, the load is entirely concentrated on the subframe, and the two do not form a rigid connection. When the vehicle is traveling on an uneven road, the compartment impacts the subframe. This repeated impact can lead to micro-cracks in the weld and gradually propagate over time.
1.3 When the compartment begins to lift, the cylinder thrust F and the pull rod tension F act concurrently on the support plate, and ultimately exert their force on the subbeam via the middle crossbeam and the support plate. If there is a deficiency in the structure at this moment, stress concentration will occur locally on the subframe, resulting in fatigue fracture. The design of the support plate and its connection with the subframe should be optimized to distribute the forces evenly and reduce the risk of stress concentration.
1.4 Currently, when users are operating the vehicles, overloading is a widespread phenomenon. It has been discovered that the rated 7.5t dump trucks are typically overloaded to about 11.5t, causing the subbeam to function under long-term overload. Zaidi ya hayo, since most units have implemented single-vehicle contracting, the vehicle is often pushed to its limits, further increasing the chance of fatigue fracture of the subframe.
1.5 There was once a weld fracture at the connection between the support plate and the middle crossbeam. At the instant of fracture, the impact force was entirely applied near the connection part of the support plate and the subbeam, inducing cracking. This constitutes a potential accident hazard and should be noted and resolved. We believe that addressing the unreasonable structure of the subframe itself is the key point, and on this premise, other factors should also be taken into consideration.
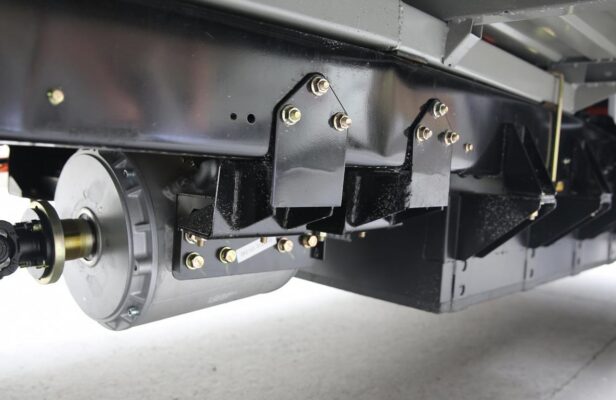
Let’s consider a real-life example to better understand the severity of these issues. Imagine a construction site where multiple XQD314OG6D 7.5T dump trucks are constantly in operation, all overloaded beyond their rated capacity. The subframes of these trucks are subjected to excessive stress on a daily basis. The uneven terrain and frequent starts and stops further exacerbate the impact and stress on the subframe and its connection with the support plate. Over time, cracks start to appear, and if not addressed promptly, it could lead to a sudden failure of the structure, potentially causing an accident and not only damaging the vehicle but also posing a threat to the safety of the driver and others on the site.
Now, let’s explore some possible process improvements to address these issues.
Firstly, in the design stage, a more robust and optimized structure for the subframe and its connection with the support plate should be developed. This could involve using advanced simulation software to analyze the stress distribution and make necessary adjustments to ensure even force application and minimize stress concentration points.
Secondly, the choice of materials for the subframe and support plate is crucial. High-strength and fatigue-resistant materials should be selected to enhance the durability and reliability of the structure. Kwa mfano, using alloy steels with improved mechanical properties can better withstand the harsh working conditions.
In terms of manufacturing processes, strict quality control measures need to be implemented. Welding procedures should be standardized and carried out by qualified welders. Regular inspections and non-destructive testing, such as ultrasonic or X-ray inspections, can help detect any potential flaws or cracks in the welds at an early stage.
When it comes to vehicle usage, it is essential to educate users about the importance of adhering to the rated load capacity. This can be achieved through training sessions and providing clear guidelines and warnings. Zaidi ya hayo, implementing a regular maintenance schedule that includes inspections of the subframe and its welds can help identify and address any developing issues before they become critical.
Let’s take another example of a fleet owner who decides to invest in process improvements. They upgrade the design of the subframe, use better materials, and enforce strict loading limits and maintenance schedules. As a result, the incidence of weld cracks and subframe failures significantly reduces, leading to lower repair costs, increased vehicle uptime, and improved safety on the job site.

In the future, as technology continues to advance, there may be opportunities to incorporate smart sensors and monitoring systems into the subframe and support plate structure. These sensors could continuously monitor stress levels, temperature, and other parameters and send real-time data to a central control unit. This would enable predictive maintenance and early detection of potential problems, further enhancing the reliability and safety of dump trucks.
Furthermore, research and development in materials science could lead to the discovery and application of even more advanced materials that offer superior strength and fatigue resistance, providing a long-term solution to the issue of weld cracks and subframe failures.
Kwa kumalizia, addressing the reasons for weld crack of the support plate of the subframe of dump trucks requires a comprehensive approach that encompasses design improvements, material selection, manufacturing quality control, user education, and regular maintenance. By taking these measures and staying abreast of technological advancements, the reliability and safety of dump trucks can be significantly enhanced, ensuring their efficient and trouble-free operation in various demanding applications.