- Common Faults and Their Causes
1.1 Difficulty in Lifting the Compartment
The reasons for this include the following aspects:
a. Insufficient oil quantity in the fuel tank;
b. Severe clogging of the fuel tank filter or pipeline;
c. Malfunction of the oil pump, no oil supply;
d. The lifting switch (connected to the atmosphere) is blocked, and the return valve of the distribution valve is stuck in the return oil position;
e. Severe imbalance of the overflow valve, leakage of the high-pressure oil pump;
f. The lifting cylinder and the limit valve are stuck, keeping the air passage to the main distribution valve connected for a long time;
g. Insufficient air pressure in the air reservoir;
h. Poor operation of the power take-off and the oil pump gears;
i. The hydraulic oil is not clean, and impurities jam the distribution valve.
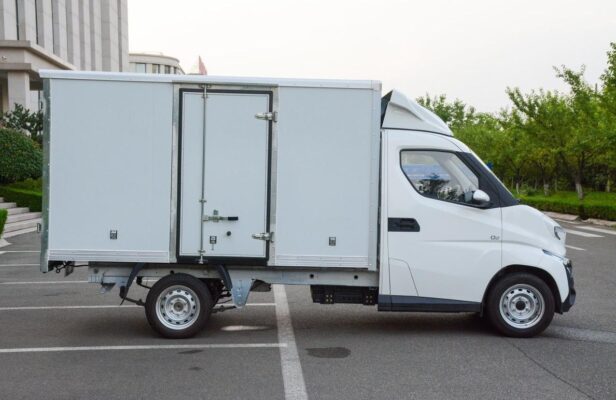
1.2 Slow Lifting of the Compartment with Jerking
The reasons are generally as follows:
a. The return oil circuit is not smooth, and the friction resistance of the lifting cylinder is too large;
b. The limit valve of the lifting cylinder is not tightly sealed, and the sealing ring of the lifting cylinder is not tightly sealed, resulting in insufficient oil pressure;
c. The working efficiency of the gear pump decreases, the oil quantity in the fuel tank is insufficient, and the gear pump cannot reach the specified oil displacement;
d. Severe clogging or leakage exists in the pipeline.
1.3 Unable to Lift with Heavy Load
The reasons are as follows:
a. Severe overloading;
b. The vehicle is parked on a ramp with a severe forward inclination;
c. The viscosity of the oil is too low;
d. Leakage faults exist in the pipeline, valve, and cylinder.
1.4 The Compartment Drops Automatically After Lifting
The reasons are as follows:
a. The one-way valve is stuck;
b. Poor sealing of the sealing ring of the lifting cylinder;
c. The distribution valve is stuck and not fully in place;
d. There is leakage in the pipeline.
1.5 The Compartment Does Not Drop
The main reason is insufficient air pressure, which prevents the return oil valve of the distribution valve from operating, or the pipeline of the limit valve is damaged, and the lifting switch and the lifting cylinder are stuck.
1.6 The Compartment Lifting Cannot Stop at Any Position
Mostly due to dirty oil, causing the non-return valve to not seal tightly, or the distribution valve and the return oil valve to not seal tightly.
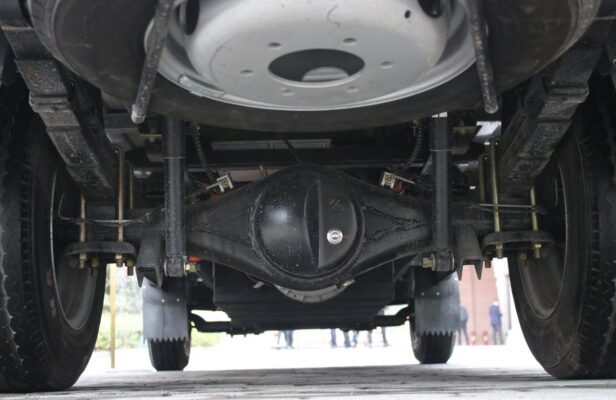
- Fault Maintenance
First, check whether there is a sufficient oil level. If not, it should be added as specified. Check whether the operation of the power take-off control mechanism is normal; check whether there are leakage phenomena in the oil and air circuits, and if necessary, check whether there are blockages. Check whether the oil pump, distribution valve, limit valve, etc. are working properly, whether the lifting cylinder is well sealed, and repair if necessary. If the various control valves of the control system malfunction, they should be replaced with new parts. When the hydraulic oil is not clean, causing blockage in the oil circuit or insufficient hydraulic pressure, and the compartment cannot be lifted in place, the hydraulic oil should be replaced. When the gear transmission mechanism or gear shaft sleeve of the oil pump is damaged, cannot operate, and has severe internal leakage, it should be replaced and repaired.
Let’s take a closer look at some of these common faults and their implications. Consider a situation where a డంప్ ట్రక్ is experiencing difficulty in lifting the compartment due to a clogged fuel tank filter. This not only delays the operation but also puts additional stress on the entire hydraulic system. If not addressed promptly, it could lead to more severe damage to the pump and other components.
In the case of slow lifting of the compartment with jerking, imagine the truck being used in a busy construction site. The inconsistent and slow lifting can significantly reduce the efficiency of the work, potentially causing delays and added costs.
Now, let’s expand on the maintenance of the hydraulic transmission system.
The wear and tear of the components within the hydraulic system, such as the journal and bearing of the gears, can have a cascading effect on the overall performance. If not detected and repaired early, the increased meshing clearance can lead to further instability and potential breakdowns. Regular inspections and preventive maintenance can help identify these issues before they escalate.
When it comes to the key points of maintaining the hydraulic system, the importance of cleanliness cannot be overstated. Even a small speck of dirt or a minute metal impurity can cause significant damage. ఉదాహరణకు, if dirt gets into a valve, it can prevent it from closing properly, leading to leaks and loss of pressure.
Suppose a technician fails to follow the proper cleaning and assembly procedures during maintenance. This could result in premature wear of the components, frequent breakdowns, and increased maintenance costs.
In another scenario, if the working oil is not selected and added correctly, it can affect the viscosity and lubrication properties, further contributing to component wear and system inefficiencies.
In the future, with advancements in technology, we may see more intelligent monitoring systems for డంప్ ట్రక్ hydraulic systems. These systems could provide real-time data on component wear, oil pressure, and temperature, allowing for predictive maintenance and minimizing downtime.
Moreover, the development of more durable and high-performance materials for hydraulic components could extend the service life and reduce the frequency of maintenance.
In conclusion, understanding the common problems of డంప్ ట్రక్s, especially those related to the hydraulic system, and adhering to proper maintenance procedures are crucial for ensuring the reliable and efficient operation of these vehicles. By being proactive in maintenance and staying updated with the latest technological developments, operators can minimize disruptions, extend the lifespan of their equipment, and improve overall productivity.
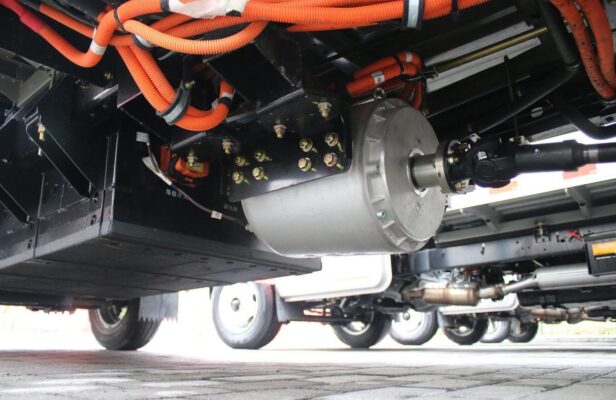
Let’s consider a real-life example of a construction company that has a fleet of డంప్ ట్రక్s. Due to a lack of a regular maintenance schedule and inadequate training for technicians, several trucks experienced frequent hydraulic system failures. This not only led to significant downtime but also affected the progress of construction projects. However, after implementing a strict maintenance program, including regular inspections, component replacements as needed, and training for technicians, the reliability of the డంప్ ట్రక్s improved significantly, reducing costs and increasing productivity.
Another example could be a డంప్ ట్రక్ owner who noticed early signs of a problem with the compartment lifting but ignored it. Eventually, the issue worsened, resulting in a major breakdown that required extensive and costly repairs.
It’s essential for operators and maintenance personnel to be vigilant and take prompt action when any anomalies are detected. This not only saves money in the long run but also ensures the safety and functionality of the డంప్ ట్రక్s.
In summary, the maintenance of డంప్ ట్రక్s is a complex but essential task that requires attention to detail, adherence to best practices, and a commitment to continuous improvement.