The power battery, being one of the core components of electric vehicles, has a direct impact on the industrialization process of electric vehicles. During actual vehicle driving, conditions such as frequent acceleration, constant speed, and deceleration changes occur, along with the external environment’s low temperatures and high heats. Relying on traditional theoretical calculations or empirical analyses is insufficient to meet the thermal management requirements of pure electric vehicles. Instead, the more mature CFD (Computational Fluid Dynamics) technology is necessary to conduct a more precise assessment and analysis of the thermal management of power batteries, reasonably optimize the internal thermal environment of the battery pack, and enhance its safety and reliability.
1. Thermal Management System Architecture and Working Principle
During the charging and discharging processes of the power battery, especially during high-current charging and discharging, the battery itself generates a temperature rise, which subsequently affects the safety performance of the battery. Additionally, uneven temperatures among different individual batteries within the battery pack can result in an uneven distribution of battery capacity and shorten the overall service life of the battery pack. These issues need to be addressed by designing an efficient thermal management system, which can, to a certain extent, reduce the energy consumption of the entire vehicle.
1.1 Thermal Management System Architecture
The thermal management system of a certain pure electric vehicle adopts a dual evaporator system, and its architecture is depicted in Figure 1. Specifically, the cooling capacity generated by the electric compressor of the pure electric vehicle is utilized to cool the battery pack through the auxiliary evaporator added inside the power battery pack, achieving the objective of simultaneously cooling the passenger compartment and the battery pack.
The dual evaporator thermal management system separates the main evaporator used for cooling the passenger compartment and the auxiliary evaporator used for cooling the battery pack from the pressure sensor via the refrigerant pipeline into two parallel branches. Each branch is equipped with an electronic expansion valve and an evaporator, enabling independent control of the two branches. To prevent excessive pressure differences between the main and auxiliary evaporators and the compressor, a pressure balancing device needs to be connected among them.
The auxiliary evaporator placed within the power battery pack achieves cooling by blowing the surrounding air with a small fan arranged on its surface. The layout diagram is presented in Figure 2.
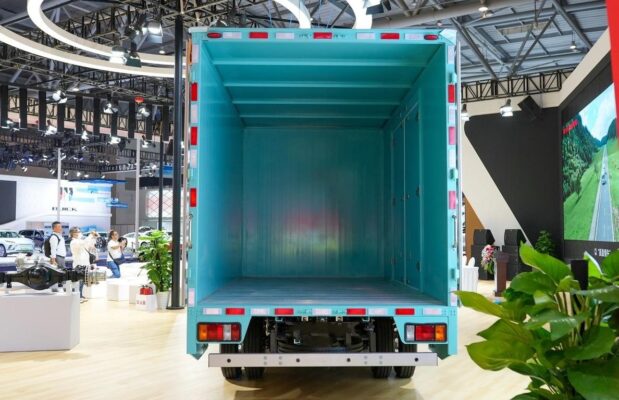
1.2 Working Principle of the Thermal Management System
The working principle of the dual evaporator thermal management system is as follows:
-
Turning on the air conditioning. The air conditioning controller initially turns on the electronic expansion valve 1 in Figure 1 based on the user’s command to activate the main evaporator. At this point, the air conditioning compressor is turned on, and the air conditioning cooling commences. Simultaneously, the air conditioning controller also receives the battery cooling demand instruction sent by the battery thermal management system. In accordance with this instruction, the air conditioning controller turns on the electronic expansion valve 2 in Figure 1 to activate the auxiliary evaporator and achieve battery cooling.
-
Turning off the air conditioning. The air conditioning controller turns off the electronic expansion valve 1 in Figure 1 as per the user’s command. At this time, if the battery thermal management cooling demand still persists, only the function of the main evaporator is deactivated. Similarly, if the battery thermal management cooling demand instruction vanishes, but the user’s cooling demand exists, only the function of the auxiliary evaporator is turned off. Only when both the electronic expansion valve 1 and 2 in Figure 1 receive the disconnection instruction does the air conditioning compressor cease operation.
2. Simulation Analysis and Verification of the Battery Thermal Management System
The high-temperature cooling method of the thermal management system of this pure electric vehicle employs an air-cooled condenser, and battery cooling is accomplished through evaporator refrigeration. Since the low-temperature heating function of the power battery utilizes another thermal management system, this article solely focuses on the high-temperature cooling of the power battery pack of the pure electric vehicle.
2.1 Establishment of the Battery System Cooling Simulation Model
-
3D model of the battery pack. Utilizing the Icepak software, the 3D model of the battery of this pure electric vehicle can be established either by self-building the model or importing a complex model. Its principal components include the battery pack housing, battery cells, battery modules, centrifugal fans, etc. To guarantee the accuracy of the analysis results, the gap between the individual cells within the module needs to be taken into account. The established 3D model of the battery pack is shown in Figure 3.
-
Fluid mathematical model. The fluid heat transfer process is constrained by the physical conservation laws, and the fundamental conservation laws encompass: the law of conservation of mass, the law of conservation of momentum, and the law of conservation of energy, among others.
The law of conservation of mass:
Where: ρ represents the density; t denotes the time; u, v, and w are the components of the velocity vector in the x, y, and z directions. cp is the specific heat capacity; T is the temperature; k is the heat transfer coefficient of the fluid; ST is the internal heat source of the fluid.
- Mesh division. Based on the established geometric model of the power battery pack, high-quality spatially closed meshes are divided using hexahedral meshes, multilevel meshes, and locally encrypted meshes. The processed mesh model is inspected for geometric errors or gaps. The divided meshes are shown in Figure 4.
2.2 Simulation Results and Analysis
2.2.1 Steady-State Simulation of Battery Pack High-Temperature Cooling
By leveraging the steady-state analysis results of the battery pack, the temperature distribution trend of the battery pack can be identified, which plays a crucial role in the design and improvement of the battery pack grouping.
It can be observed from the internal trace distribution of the battery pack in Figure 5 that the fluid distribution of the battery pack is relatively uniform.
It can be discerned from the steady-state temperature distribution of the battery pack high-temperature cooling in Figure 6 that the trace analysis is reasonable, and the temperature in the area where the fluid distribution of the battery pack is uniform is also relatively uniform.
2.2.2 Transient Simulation of Battery Pack High-Temperature Cooling
Conducting a transient analysis of the battery pack is closer to the actual situation and can verify the accuracy of the simulation analysis through experiments (see Figure 7).
The high-temperature cooling environment temperature of the battery pack is 40°C, the temperature at the air inlet of the battery pack is 19°C, and 1C discharge is adopted. Through the transient analysis of the battery pack, the maximum temperature difference of the battery pack during 1C discharge for 1 hour is 7.1°C, and the maximum temperature is 37.2°C, which complies with the high-temperature cooling requirements of thermal management.
2.3 Experimental Verification of Power Battery Cooling
Position the entire vehicle within the environmental chamber and set the environmental temperature to the limit temperature during the battery pack simulation. The thermal management test can be initiated when the temperature of the environmental chamber meets the test requirements.
A total of 5 temperature acquisition points (T1~T5) are arranged on the body of the power battery pack of a certain pure electric vehicle. Before the test commences, the test instruments need to be installed, the vehicle status confirmed, and the vehicle started for preheating; the vehicle doors and windows are closed, and the air conditioning is turned on; the air conditioning mode is selected as the face air mode, the air conditioning temperature is set at 24°C, and the wind speed is adjusted to the middle gear; after approximately 30 minutes of preheating, the vehicle enters the maximum speed operation state, the test begins, and the temperature at each temperature measurement point is recorded. The data is measured every 5 minutes, and the test results are shown in Table 1.
Before and after the test, the maximum temperature of the power battery is 57°C, and the test time is approximately 65 minutes. Within any 30 minutes after the start of the test, the maximum temperature rise of each individual cell of the battery pack is ≤ 22°C, the average temperature rise of each individual cell is ≤ 20°C, the average temperature difference of each individual cell is ≤ 12°C, and the maximum temperature of the battery pack is ≤ 60°C, all fulfilling the design indicators.
3. Conclusion
The research on the battery thermal model constitutes an important aspect of the battery thermal management design process. The dual evaporator structure design satisfies the thermal management requirements of pure electric vehicles. Utilizing the Icepak software for thermal management simulation analysis can reflect the temperature distribution trend of the battery pack, and the disparity between the analysis results and the test data is minimal. This indicates that the application of Icepak in the simulation analysis of new energy electric vehicle battery packs is feasible and plays a guiding role in the determination of the number and location of temperature sensor arrangements.