The damage of the rocker arm is predominantly manifested in the wear of the rocker arm head. During the inspection process, the rocker arm head ought to be smooth and devoid of any damage. The depression following repair should not exceed 0.50mm. In the event that it surpasses the stipulated limit, repair is necessary, and the common repair approaches include surfacing and grinding.
Check our Latest products!
Електричний рефрижератор
Електричний рефрижератор
Електричний рефрижератор
Електричний рефрижератор
Електричний рефрижератор
Електричний рефрижератор
Електричний рефрижератор
Електричний рефрижератор
Repair of the rocker arm shaft and rocker arm: The main form of damage to the rocker arm is the wear of the rocker arm head. During the inspection, the rocker arm head should be smooth and without any impairments. The depression after repair should not be greater than 0.50mm. If it exceeds the regulation, it is necessary to undertake repairs. The feasible methods could be surfacing and grinding. If the fit clearance between the rocker arm and the rocker arm shaft exceeds the prescribed limit, the bushing should be replaced and reamed or bored for repair in accordance with the size of the shaft. When inserting the bushing, it is essential to ensure that the oil hole of the bushing aligns with the oil hole on the rocker arm to prevent any adverse impact on lubrication. When the threaded hole of the adjusting screw on the rocker arm is damaged, it should typically be replaced. When the wear of the journal of the rocker arm shaft is greater than 0.02mm or the fit clearance between the rocker arm shaft and the bearing hole of the rocker arm exceeds the regulation, it can be remedied through brush plating or replacement. The rocker arm shaft that is bent should be straightened by cold pressing to ensure that its straightness error does not exceed 0.03mm within a length of 100mm.
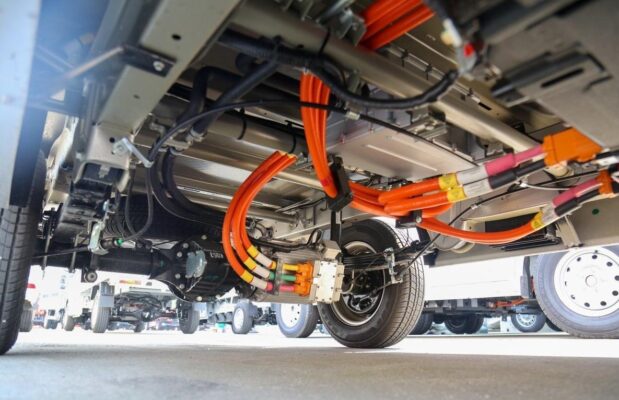
Assembly of the rocker arm mechanism. The rocker arm is assembled on the cylinder head and it is composed of the rocker arm, rocker arm shaft, spring and rocker arm shaft support, among other components. After engine maintenance, the key points for assembling the rocker arm mechanism are as follows. Firstly, thoroughly clean and dry the rocker arm, rocker arm shaft, support and other parts, and meticulously check whether the oil holes of these components are unobstructed. Subsequently, apply a layer of oil on the rocker arm shaft and install the rocker arm support, rocker arm, positioning spring and other parts on the rocker arm shaft in the prescribed sequence. The oil groove on the rocker arm shaft should face downward, and the oil outlet hole should be upward and to the left side of the engine, that is, on the side of the intake and exhaust channels. Incorrect installation in the reverse direction would result in poor lubrication of the rocker arm mechanism. Then, insert the push rod into the tappet concave seat and loosen the valve clearance adjustment bolt on the rocker arm to avoid bending the push rod when tightening the support bolt. Finally, uniformly tighten the rocker arm mechanism from the middle to both ends to reach the specified tightening torque (generally 29-39 Н·м). After tightening, the rocker arm should be capable of rotating flexibly.
Beyond the basic repair and assembly procedures mentioned earlier, there are several additional considerations and advanced techniques that can further enhance the reliability and performance of the rocker arm and rocker arm shaft in a dump truck engine.
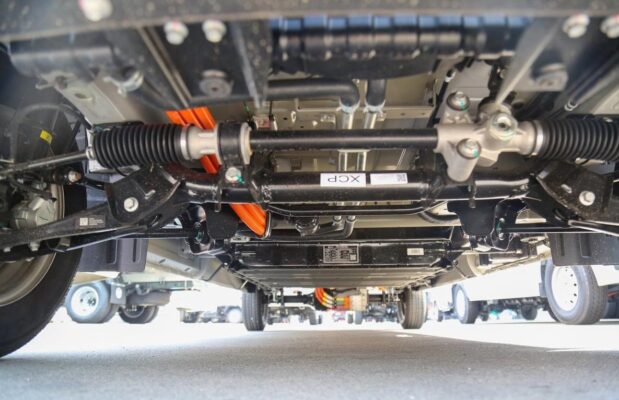
When undertaking the surfacing process for the rocker arm head, it is crucial to select the appropriate welding material that matches the base metal’s properties. This ensures a strong and durable bond that can withstand the rigors of engine operation. Додатково, the grinding operation should be carried out with precision equipment to achieve the desired surface finish and dimensional accuracy.
In cases where the wear on the rocker arm shaft is significant, rather than simply relying on brush plating or replacement, advanced processes such as thermal spraying or laser cladding can be employed. These techniques offer superior wear resistance and can extend the service life of the shaft.
When replacing the bushing, it is not just a matter of fitting a new one. The quality and material of the bushing should be carefully selected to match the operating conditions and loads of the dump truck. Some high-performance bushings may incorporate self-lubricating materials or special coatings to further improve lubrication and reduce friction.
During the assembly process, proper torque application is not the only critical factor. The alignment and concentricity of the various components also play a vital role. Using specialized alignment tools and fixtures can ensure that the rocker arm, shaft, and support are precisely positioned, minimizing stress concentrations and potential wear points.
Let’s consider a scenario where a maintenance technician overlooked a minor crack in the rocker arm during inspection. З часом, this crack propagated, leading to a sudden failure of the rocker arm during engine operation. This not only caused engine damage but also led to costly downtime and repair expenses.
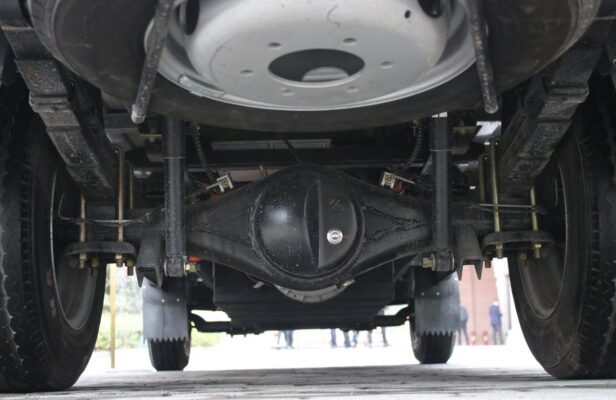
On the contrary, a well-trained and meticulous technician who paid attention to every detail during the repair and assembly process could significantly extend the lifespan of the rocker arm mechanism. For instance, by precisely grinding the rocker arm head to the exact specifications and ensuring proper alignment of all components, the engine’s performance and reliability could be optimized.
The lubrication system associated with the rocker arm and shaft is another area that requires in-depth understanding. The type and viscosity of the lubricating oil, as well as the frequency of oil changes, can have a profound impact on the longevity of these components. Using high-quality synthetic lubricants and adhering to a strict oil change schedule can prevent premature wear and damage.
In modern engine designs, some dump truck engines may incorporate variable valve timing or other advanced technologies that affect the operation and maintenance of the rocker arm mechanism. Technicians need to stay updated with these technological advancements and have the appropriate tools and knowledge to handle such systems.
Furthermore, the use of non-destructive testing methods such as magnetic particle inspection or ultrasonic testing can provide a more comprehensive assessment of the condition of the rocker arm and shaft. These techniques can detect hidden flaws or internal cracks that might not be visible during a visual inspection.
На закінчення, the repair and assembly of the rocker arm and rocker arm shaft of a dump truck engine is a complex task that demands a combination of technical expertise, attention to detail, and the use of appropriate tools and materials. By adhering to best practices and continuously learning and adapting to new technologies, technicians can ensure the efficient and reliable operation of the engine, minimizing breakdowns and maximizing the vehicle’s productivity.
In the future, as engine technologies continue to evolve and become more sophisticated, the maintenance and repair of components like the rocker arm and shaft will likely require even higher levels of precision and specialized skills. This will drive the development of more advanced training programs and diagnostic tools to meet the demands of the industry.
Наприклад, the integration of artificial intelligence and machine learning in engine diagnostics could provide real-time monitoring and predictive maintenance capabilities. This would enable technicians to identify potential issues with the rocker arm mechanism before they escalate into major failures.
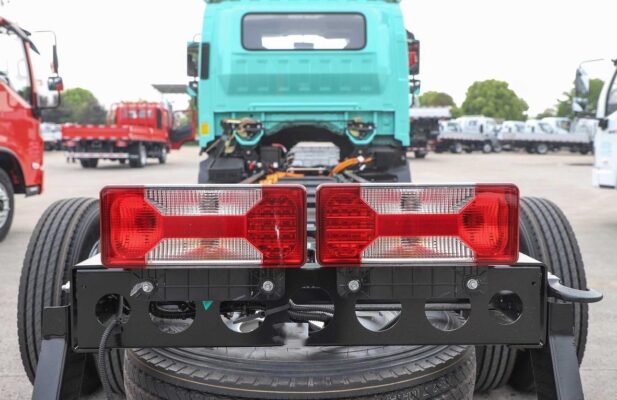
Moreover, the development of lightweight and high-strength materials for rocker arms and shafts could offer improved performance and fuel efficiency in dump truck engines. Однак, these new materials may also present unique challenges in terms of repair and assembly, requiring technicians to stay at the forefront of technological innovation.
In summary, the field of rocker arm and rocker arm shaft repair and assembly in dump truck engines is constantly evolving, and those involved in this aspect of vehicle maintenance must remain committed to ongoing learning and improvement to keep pace with the changing landscape.