New energy vehicles have gained significant popularity, and new energy vans are increasingly utilized in some cities with license plate and number restrictions. Their sales are steadily improving, but what about their quality? What are the common faults associated with new energy vans?
-
Brake system failure. This is among the most frequently encountered faults. Brake failure does not imply a complete absence of brakes but rather the lack of brake assistance. Hence, when confronted with such a fault, it is essential to apply significant force to the brake pedal. We have previously analyzed in another article why the brake system of electric vehicles has such a high failure rate and will not elaborate further here.
-
Battery failure. Although battery technology has witnessed substantial breakthroughs and can essentially meet the requirements of urban express logistics in terms of energy density and range, the failure rate of electric vans remains higher compared to gasoline vans. The primary issue lies in the excessive pressure difference among individual cells. אַדדיטיאָנאַללי, there are problems such as poor sealing of the battery pack, which leads to water ingress or water vapor causing insulation alarms. Battery cell leakage is infrequent but does occur. Other faults might also arise in the BMS management system or during the transmission of temperature and voltage signals.
-
Motor and controller failures. These are mainly manifested by overheating and self-protection of the motor or motor controller. The motor might burn out, and there could be gear meshing issues between the motor and the rear axle differential. Problems on the lines, such as engagement and pin contact, can also arise.
-
Rear axle differential. This fault is highly prevalent in a specific type of electric van. Since the motor directly drives the differential, and the quality of the differential is subpar, it often results in gear meshing problems. In some instances, the teeth on the drive shaft are directly worn smooth, preventing the transmission of power to the tires altogether.
-
DCDC converter. This fault is also quite common. The main characteristic is that the small battery loses power, leading to inability to start the vehicle, non-functional lights, silent horns, and inoperative radios, among other issues. The primary function of the DCDC is to convert the high voltage of the large battery into the low voltage of the small battery to charge the latter.
-
Line matching problems. This fault does not occur frequently. אָבער, when it does, it poses a significant challenge for mechanics. The troubleshooting process is not straightforward. If there are also communication protocol issues, personnel from the supporting enterprises need to be dispatched for repairs.
-
Range problem. In fact, this is a well-known issue. Recently, it has been brought to the forefront. It has become an industry norm for manufacturers to overstate or mark the range based on working conditions. If the battery attenuation has reached a certain extent, one can still apply for the manufacturer’s three-package guarantee.
-
Other faults will not be elaborated. As they are similar to those of gasoline vehicleס, repair shops can typically handle them. אָבער, some repair shops are reluctant to undertake repairs upon hearing that it is an עלעקטריק פאָרמיטל. This is unnecessary. After all, apart from the high-voltage component, the other faults are comparable to those in gasoline vehicleס.
Now, let’s delve deeper into these faults and explore some potential solutions and preventive measures:
For the brake system failures, regular inspections and maintenance of the braking components, including brake pads, calipers, and the brake fluid, are crucial. Upgrading the brake system software and firmware to address any known issues can also help improve reliability.
In terms of battery failures, manufacturers could invest in more rigorous quality control during the production process to minimize cell pressure differences and ensure better sealing of the battery packs. פאָרמיטל owners can also follow proper charging and discharging practices to extend the battery’s lifespan.
To prevent motor and controller failures, adequate cooling systems and regular checks of the motor’s insulation and electrical connections are necessary. Monitoring the temperature and performance of the motor and controller during operation can help detect potential issues early.
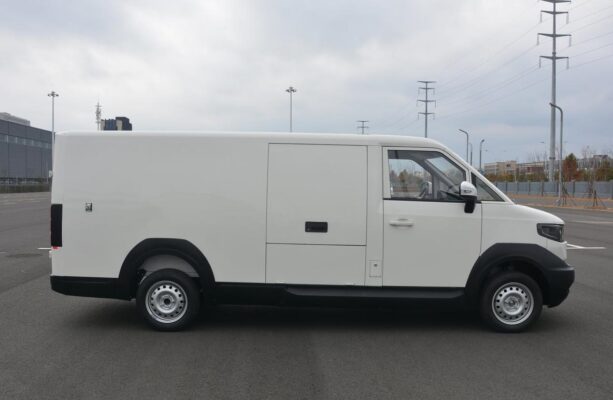
When it comes to the rear axle differential, improving the design and manufacturing quality of the differential, as well as regular lubrication and inspection, can reduce the occurrence of gear meshing problems.
For DCDC converter faults, using high-quality components and conducting thorough testing during the manufacturing stage can enhance the reliability of the converter. אַדדיטיאָנאַללי, real-time monitoring of the converter’s performance can facilitate prompt detection and repair of faults.
Regarding line matching problems, manufacturers should ensure better quality control during the vehicle assembly process and adhere to strict communication protocol standards. Training mechanics in advanced diagnostic tools and techniques specific to new energy vehicle lines can also improve the efficiency of fault identification and repair.
As for the range issue, manufacturers need to be more transparent and accurate in their range claims and provide consumers with clear information on factors affecting the actual range. At the same time, ongoing research and development in battery technology to improve energy storage and efficiency will help address this concern in the long run.
אין מסקנא, while new energy vans come with their set of common faults, with continuous technological advancements, improved manufacturing processes, and proper maintenance and usage by consumers, the reliability and performance of these vehicles can be significantly enhanced, making them a more viable and sustainable option for urban transportation.